Austenitic Chromium-Manganese Stainless Steels
A European Approach
Extensive data on the newly-designed 1.4618 grade has been presented. It is concluded that grade 1.4618, as a representative of the 200 series, has an optimum chemical composition that makes it less dependent on alloy-surcharge cost fluctuations while obtaining mechanical and corrosion resistance properties similar to those of grades 1.4301 (304) and 1.4310 (301). Reprinted from Euro Inox with permission.
Authors
J. Charles, La plaine Saint Denis, France
A. Kosmač, Brussels, Belgium
J. Krautschick, Krefeld, Germany
J. A. Simón, Los Barrios (Cádiz), Spain
N. Suutala, Espoo, Finland
T. Taulavuori, Tornio, Finland
1 Introduction
Replacing nickel in austenitic stainless steels by adding manganese has been considered for over 50 years. The purpose is to reduce the impact of nickel-price fluctuations on the alloy surcharge. This has resulted in the development of the so-called 200 series. These grades also have complementary nitrogen additions, to further stabilise the austenitic phase and provide high-strength properties necessary in certain applications. Copper has also been successfully added, to provide austenite stabilisation and improve cold- forming properties. When copper is added, nitrogen content can be reduced, providing softer manganese austenitic grades.
In Europe and North America, these grades had only limited applications until the end of the last century. They were selected mainly for their combination of high strength and ductility, for example in the production of conveyor belts.
In India, due to restrictions on nickel imports, type 200 stainless steels have been extensively used since the 1980s, essentially for affordable stainless steel tableware. As these items are typically washed by hand and not exposed to the more corrosive conditions of dishwashers, their corrosion resistance has proved entirely adequate.
More recently, large amounts of type 200 stainless steels have been produced in Asia. Some of the grades developed have not met current international standards, since they have been designed to minimize alloying elements – including chromium, which is a key element in corrosion resistance. The lack of international standards and references for these grades has recently been pointed out, along with:
- an over-generalised use of these grades as a supposed alternative to grade 1.4301 (304);
- the emergence of other type 200 steels with low Cr and Ni contents, high levels of impurities and ill-defined mechanical properties;
- the fact that the non-magnetic nature of these grades means customers can easily mistake them for austenitic chromium-nickel grades.
In Europe, the wish to be less affected by the alloy surcharge has resulted in the develop- ment of the ferritic grades. However, these are more difficult to weld, especially beyond a thickness of 6 mm. In some applications, non-magnetic – i.e. austenitic – material is preferable. It was therefore desirable to make available a type 200 stainless steel with:
- an adequate and consistent level of corrosion resistance;
- mechanical properties that make it easier to form than the “classic” grade 1.4372 (201).
For CrMn stainless steel to become more acceptable in a European environment, a high level of standardisation is required. providing technical information has been made a priority, to avoid misunderstandings and improper use.
To respond to these needs, a working group with representatives of the main European flat stainless steel producers was created, under the umbrella of Euro Inox. Its main conclusions are presented in this publication.
2 History of the 200 series and current developments
The 200 series of stainless steels was developed in the early 1930s. Although the first chemical analyses were of the 205 kind (Ni content close to 1 % and stabilisation of the austenitic phase by simultaneous high manganese and nitrogen additions – see Figures 1 and 2), the first grades to receive the AISI label in the mid-1950s were the 201 and 202 grades (nickel content around 4–6 % and nitrogen additions below 0.25 %). These became more popular during the Korean War, due to the need to conserve nickel. At that time, the use of nickel was mainly restricted to military applications. grade 214, with less than 1 % Ni and about 0.35 % N was produced at the end of the 1950s. Austenitic CrMn grades containing Mo to improve corrosion resistance appeared in the mid- 1960s, both in the u.S. and Europe.
Simultaneously, Mn and Cu containing grades were developed which made it possible to produce 4–6 % Ni austenitic grades (grades 211 and 203) with relatively low nitrogen content (<0.06 % N). Drawing properties equivalent to those of 304 could be achieved. Due to a new Ni shortage, these grades began to be popular in the early 1970s. The new AOD technology made adding nitrogen to the 200 series easier and more cost-effective (Table 1). Once again the nickel shortage ended and, with high availability, Ni prices went down again. For more than 30 years, grade 304 was the standard of the stainless steel family, at an average yearly growth of 5–6 %.
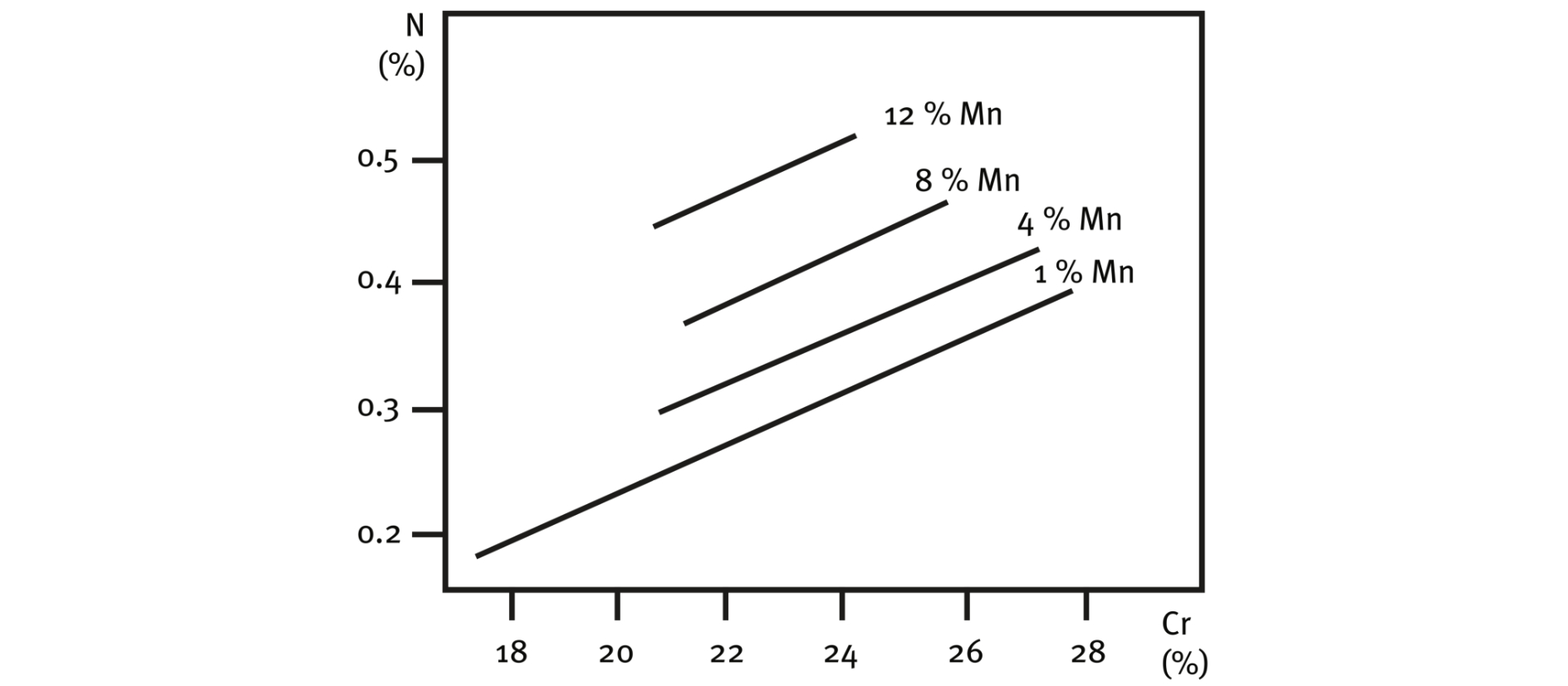
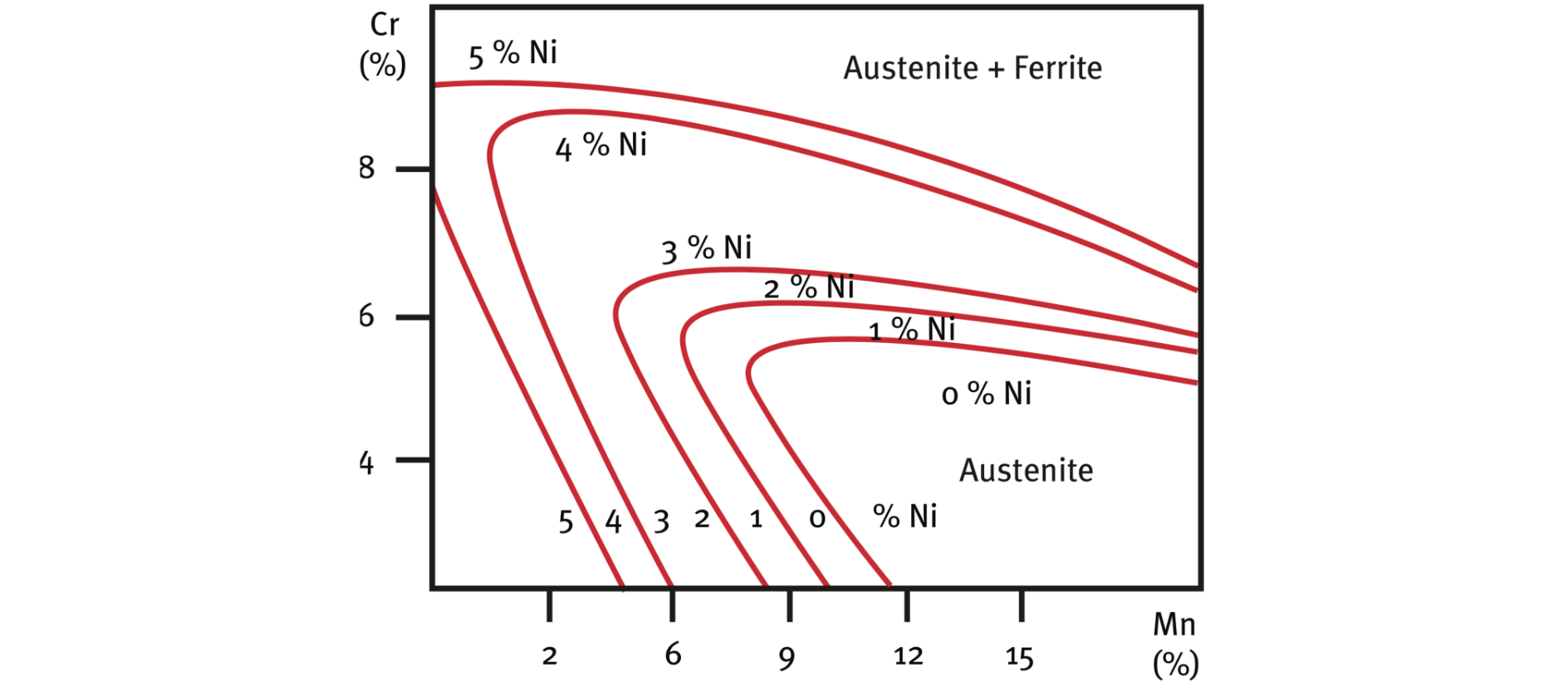
The 200 series still had only marginal applications in the eighties and nineties (with the exception of India). With the new century, a new period of high nickel-price volatility began. China, especially, became a major user of 200 series stainless steel. Austenitic CrMn steel was produced locally, the rest being imported mainly from India.
AISI1 | UNS2 | Cr | Ni | Mn | N | C | S | Others |
---|---|---|---|---|---|---|---|---|
201 | S20100 | 16.0–18.0 | 3.5—5.5 | 5.5—7.5 | 0.25 max. | 0.15 max. | 0.030 max. | |
S20103 | 16.0–18.0 | 3.5—5.5 | 5.5—7.5 | 0.25 max. | 0.03 max. | 0.030 max. | ||
201lN | S20153 | 16.0–17.5 | 4.0—5.0 | 6.4—7.5 | 0.10—0.25 | 0.03 max. | 0.030 max. | Cu 1.0 max. |
S20161 | 15.0–18.0 | 4.0—6.0 | 4.0—6.0 | 0.08—0.20 | 0.15 max. | 0.040 max. | ||
202 | S20200 | 17.0–19.0 | 4.0—6.0 | 7.5—10.0 | 0.25 max. | 0.15 max. | 0.030 max. | |
203 | S20300 | 16.0–18.0 | 4.0—6.0 | 5.0—6.5 | - | 0.08 max. | 0.18—0.35 | Cu 1.75—2.25 |
204 | S20400 | 15.0–17.0 | 1.5—3.0 | 7.0—9.0 | 0.15—0.30 | 0.03 max. | 0.030 max. | |
S20430 | 15.5–17.5 | 1.5—3.5 | 6.5—9.0 | 0.05—0.25 | 0.15 max. | 0.030 max. | Cu 2.0—4.0 | |
205 | S20500 | 15.5–17.5 | 1.5—3.5 | 14.0—15.5 | 0.32—0.40 | 0.12—0.25 | 0.030 max. | |
214 | S21400 | 17.0–18.5 | 1.0 max. | 14.0—16.0 | 0.35 min. | 0.12 max. | 0.030 max. | |
216 | S21600 | 17.5–22.0 | 5.0—7.0 | 7.5—9.0 | 0.25—0.50 | 0.08 max. | 0.030 max. | Mo 2.0—3.0 |
S21603 | 17.5–22.0 | 5.0—7.0 | 7.5—9.0 | 0.25—0.50 | 0.03 max. | 0.030 max. | Mo 2.0—3.0 | |
S24000 | 17.0–19.0 | 2.25—3.75 | 11.5—14.5 | 0.20—0.40 | 0.08 max. | 0.030 max. | ||
EN3 | Cr | Ni | Mn | N | C | S | Others | |
14371 | 16.0–17.0 | 3.5—5.5 | 6.0—8.0 | 0.15—0.20 | 0.03 max. | 0.015 max. | ||
14372 | 16.0–18.0 | 3.5—5.5 | 5.5—7.5 | 0.05—0.25 | 0.15 max. | 0.015 max. | ||
14373 | 17.0–19.0 | 4.0—6.0 | 7.5—10.5 | 0.05—0.25 | 0.15 max. | 0.030 max. |
Table 1 . Chemical analyses of different austenitic CrMn grades in % by mass (200 series)
1AISI = American Iron and Steel Institute designations
2UNS = Unified Numbering System designations
3EN = EN 10 088-2 designations
3 The new 200 European grade: 1.4618
While technical development determines a material’s potential, economic factors often decide its market success. The most relevant economic factor over the last ten years has been the volatility of raw-material prices – especially that of nickel. In applications with strong inter-material competition, where several materials can qualify for the same end-use, price factors usually tip the balance.
In the case of the 200-series grades, designed to substitute the classical 300 series (grades mainly characterized by good corrosion resistance, low yield strength and high formability properties), the market lacked a well defined, standardised offer. Most of the developed grades were under alloyed, when considering general or localized corrosion resistance, or suffered from increased sensitivity to delayed crack-ing and stress corrosion cracking.
The newly-developed austenitic CrMn grade (with 16.5 % Cr min.; 4.5 % Ni min.) is designed to obtain an optimum compromise between cost reduction (lower nickel), high formability and the achieving of corrosion resistance as close as possible to that of 1.4301. Improvements in melting practices have made it possible to reduce carbon content and add nitrogen, which improves formability. Drawability is further increased by copper alloying.
Table 2 shows the 1.4618 specification, agreed by European stainless steel producers. The grade meets the “rich side” of the AISI 201 specification and is further alloyed with copper.
Steel number | 14618 |
---|---|
Steel name | X9CrMnNiCu17–8–5–2 |
Chemical composition | C <0.10, Si <1.00, |
(% by mass) | Mn 5.50–9.50, P <0.070, |
S <0.010, Cr 16.50–18.50, | |
Ni 4.50–5.50, Cu 1.00–2.50, | |
N <0.15 | |
Rp0.2 (Mpa) min. | 220 |
Rm (Mpa) | 520–850 |
A80 (%) min. | 40 |
KV (J) min. | 100 |
Table 2. Chemical composition and mechanical properties of 1.4618
The new grade 1.4618 also falls within the analysis band of grade 201. however, it is distinct from grade 1.4372 in three respects:
- It is on the “rich side” of the 201 composition band, which is beneficial to its corrosion resistance.
- It is low in allowable sulphur content, which further improves corrosion resistance.
- Copper is added for metallurgical reasons, to obtain mechanical properties close to those of grade 1.4301 (304) in terms of elongation to rupture. however, the yield strength of the 200 series is higher than that of the 300 series.
Being new, the grade is not yet included in standard EN 10088–1:2005. until the next revision of EN 10088–1, certificates can be supplied by the mills according to ASTM A 240 grade 201 and the agreement of the customer on copper content.
4 Mechanical properties
Figure 3 shows typical mechanical properties of 1.4618. Grade 1.4618 behaves similarly to 1.4310 (301) austenitic grade – i.e. its yield strength (Rp0.2) is slightly higher than that of grade 1.4301 (304).
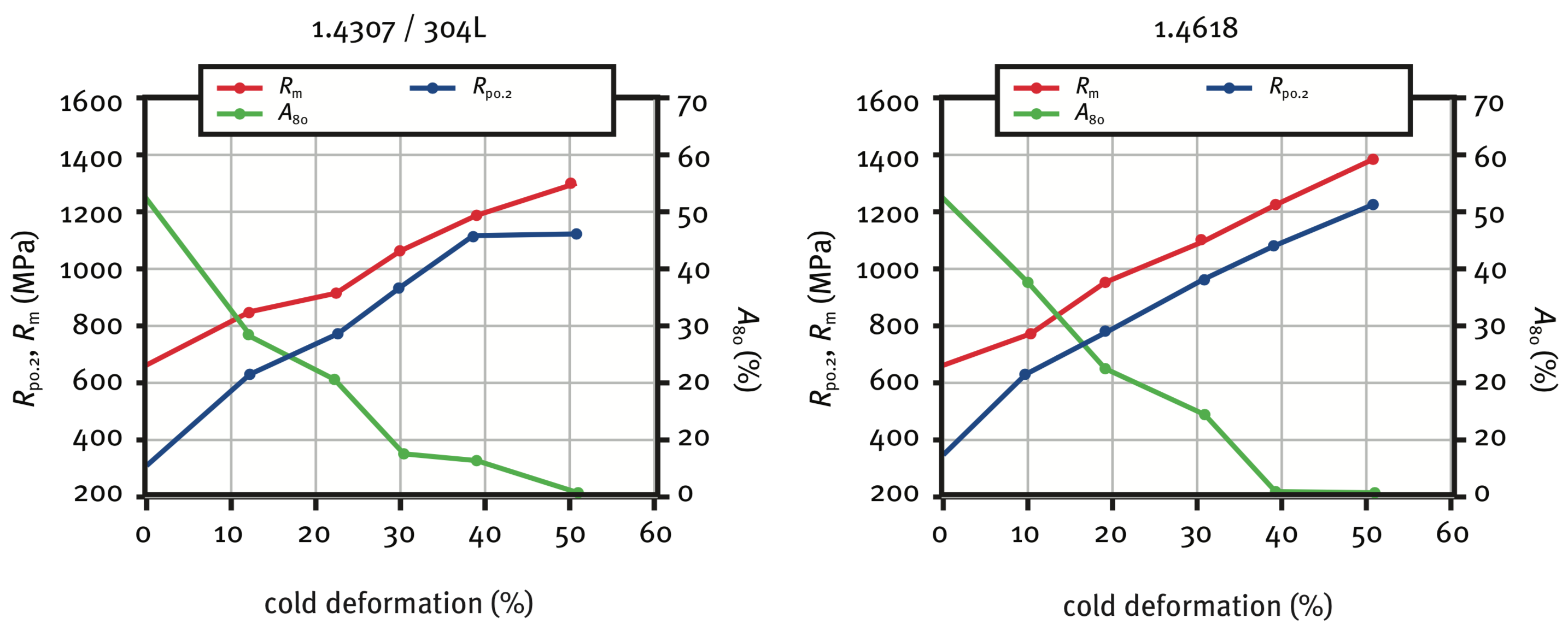
Mechanical properties remain very similar, although grade 1.4618 shows slightly high- er mechanical properties in the cold worked state than 1.4307 (304l).
In certain environments, grade 1.4618 is sometimes considered as a lower-cost alternative to 1.4301 or 1.4307. Figures 4 and 5 show that in terms of mechanical properties, 1.4618 is similar to 1.4301 (304) and 1.4307 (304l) and much softer than 1.4372 (201).
Figure 4 shows that 1.4618 has much lower Rp0.2 and Rm than 1.4372 (201) and that formability is improved. Furthermore, when cold deformed, alloy 1.4618 exhibits a very stable austenitic structure, being less sensitive to martensitic phase transformation than CrNi austenitic grade 1.4307.
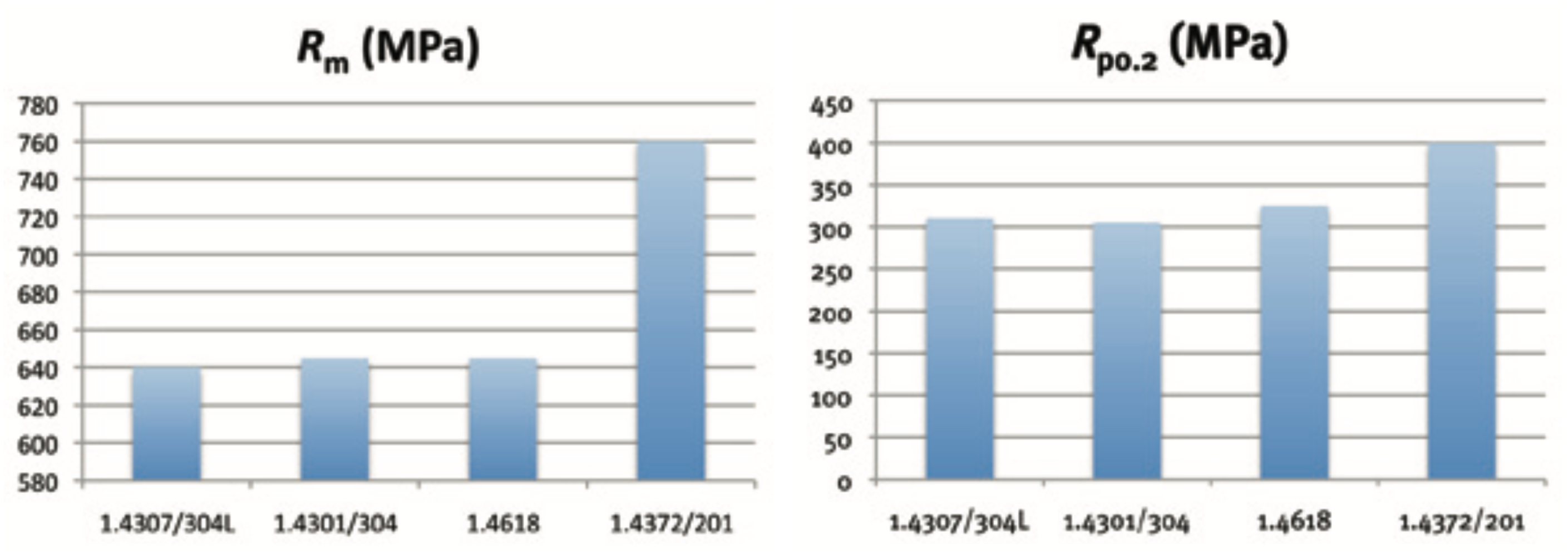
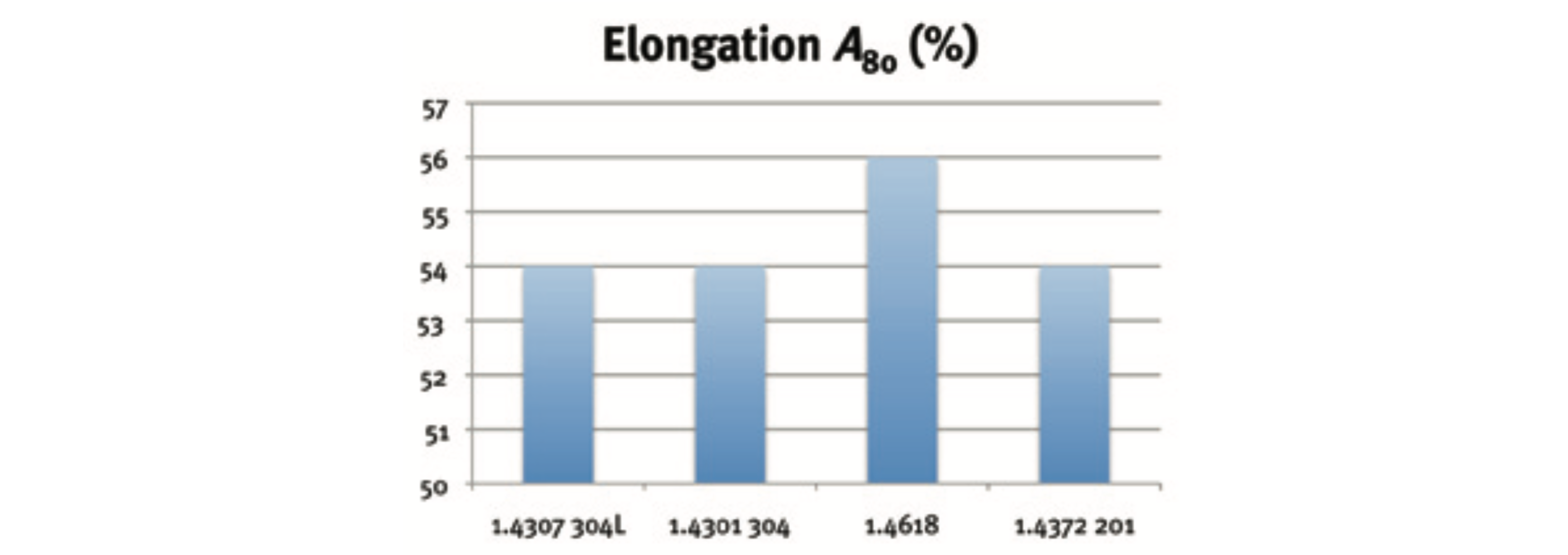
One of the factors determining the formability of a steel grade is its alloying composition. The characteristics affecting the formability of stainless steel include yield strength, tensile strength, ductility and the effect of work hardening on these proper- ties. The yield strength of 1.4618 is modest and only slightly higher than that of austenitic CrNi grades. The drawing ratio, however, is comparable to that of austenitic CrNi grades.
Typical room temperature and sub-zero temperature mechanical properties are presented for 1.4372, for general information. Tensile strength increases substantially with decreasing temperature and this effect can also be found with chromium-nickel austenitic stainless steels. Yield strength also increases, but to a lesser extent.
Some reduction in ductility can be observed, as measured by elongation. however, ductility values remain high down to –100 °C.
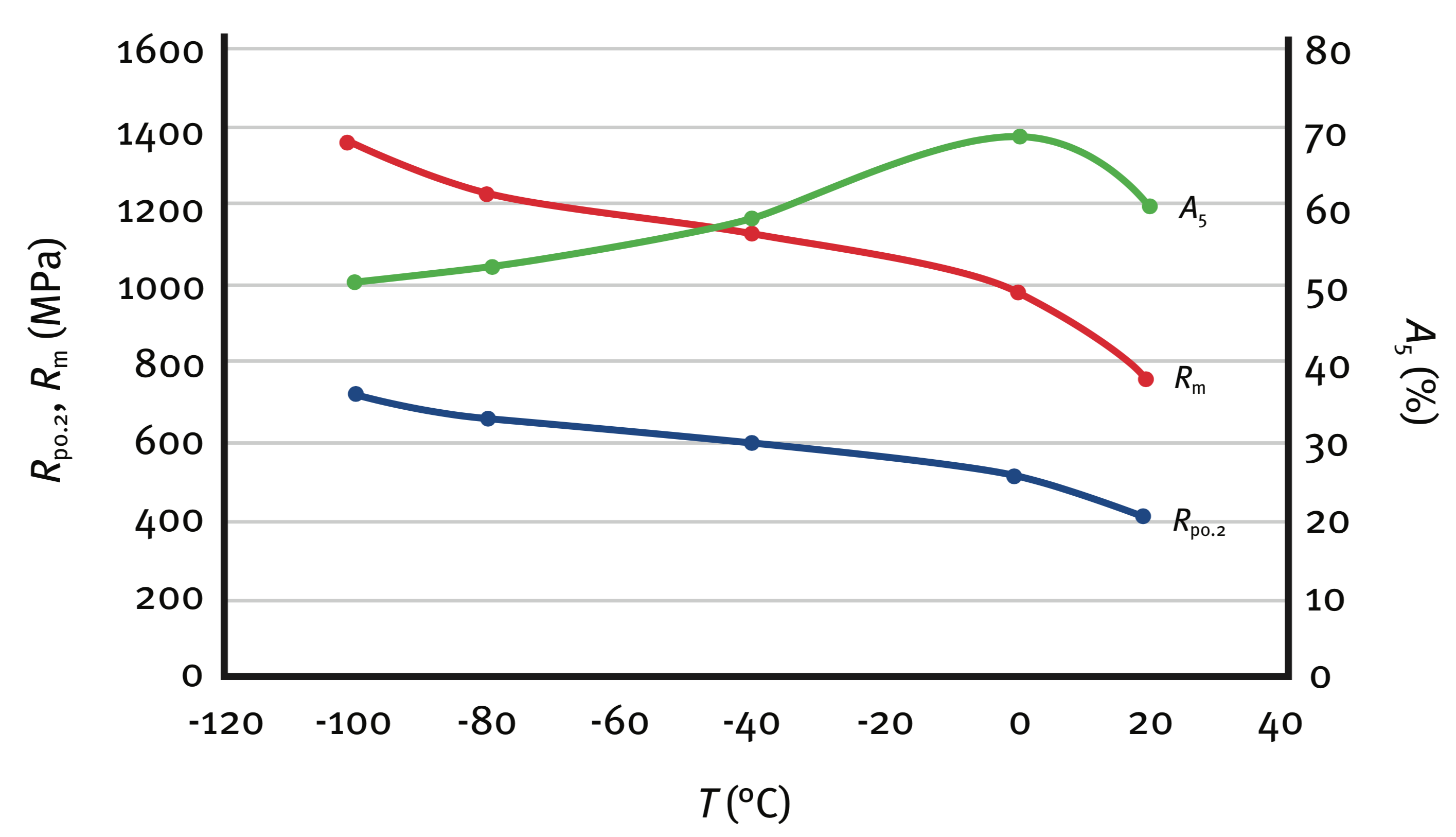
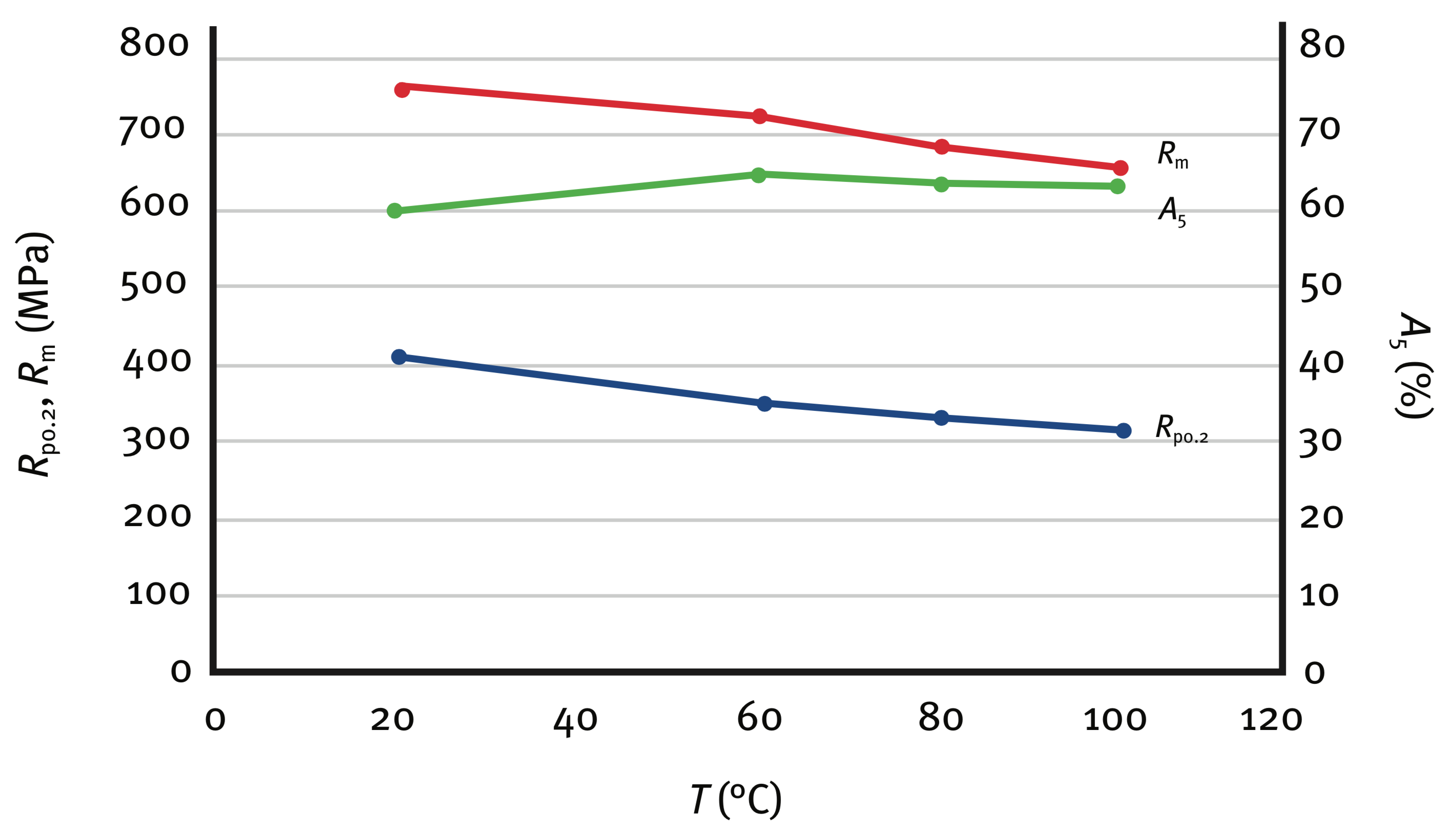
For some applications, the effect of subzero temperatures must also be considered in materials selection. Austenitic stain- less steels are very often used in sub-zero temperature applications. It is important for safe service that a high level of fracture toughness is maintained at all exposure temperatures.
Like all austenitic stainless steel, 1.4618 has exceptional toughness and does not exhibit the ductile to brittle transition temperature (DBTT) behaviour that characterises ferritic and martensitic stainless steels. The variation of impact toughness with temperature is therefore minor and the steel can be successfully used at sub-zero temperatures. Figure 7 shows impact toughness results at different temperatures.
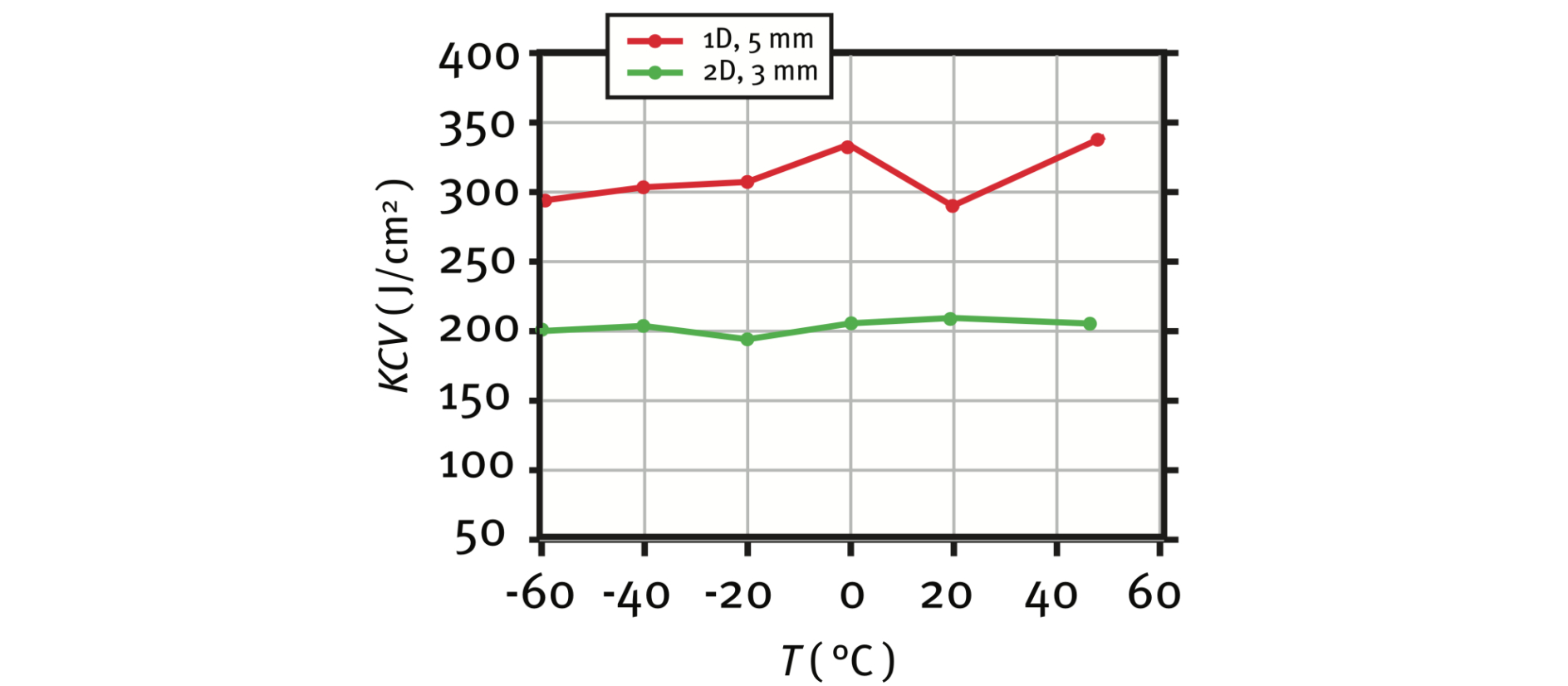
5 Formability
Austenitic stainless steels are almost without exception well suited to deep-drawing operations. The most important properties affecting drawability are yield strength, tensile strength and ductility. Composition is another important factor. In general, higher nickel and copper content improves drawability. This is also why 1.4618 performs very well in terms of formability.
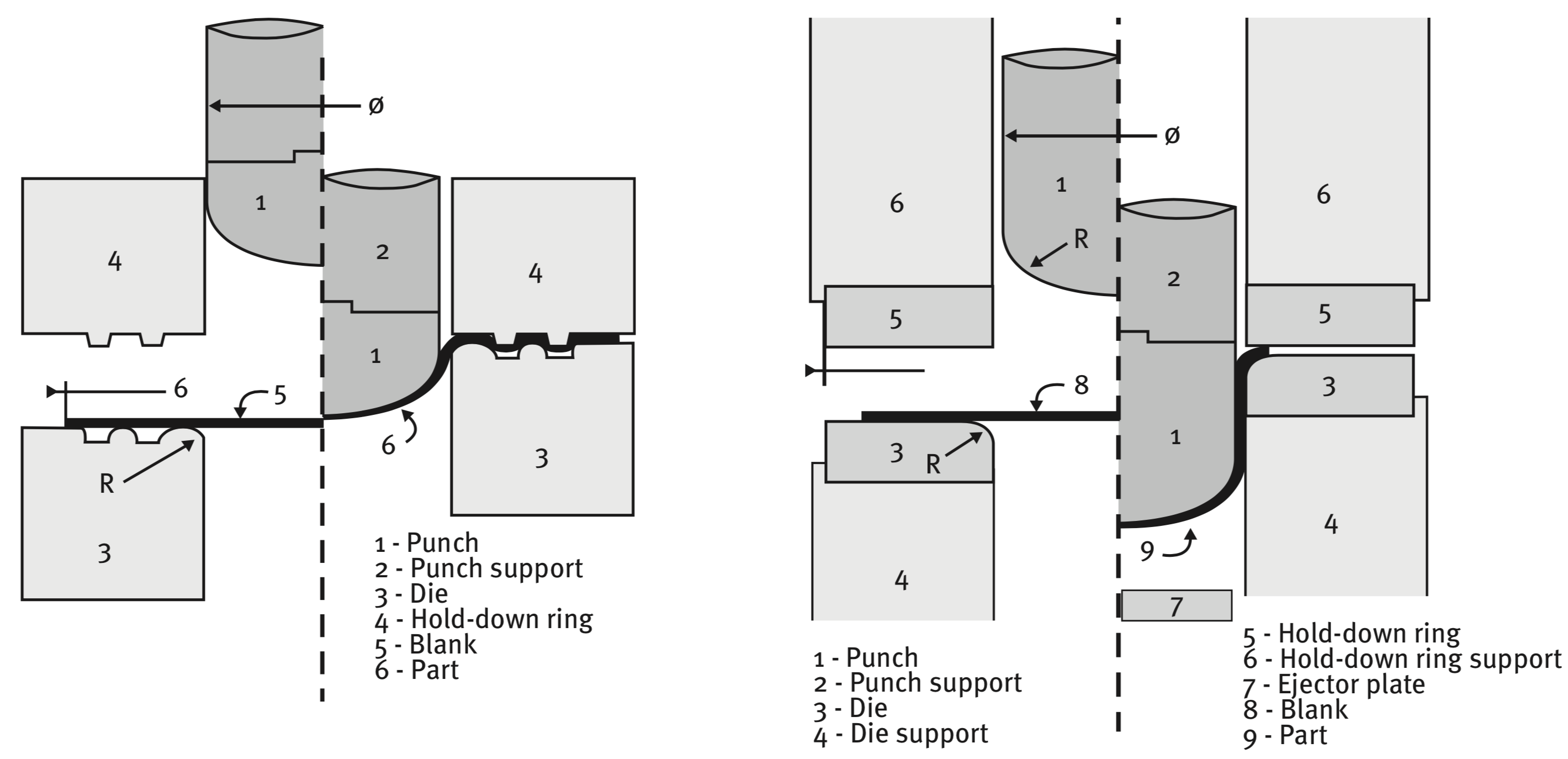
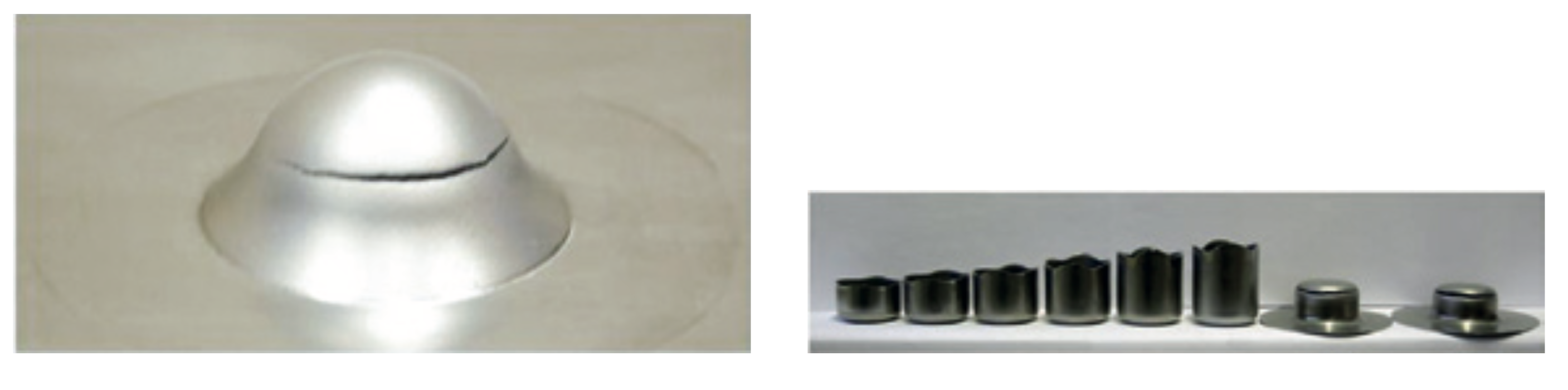
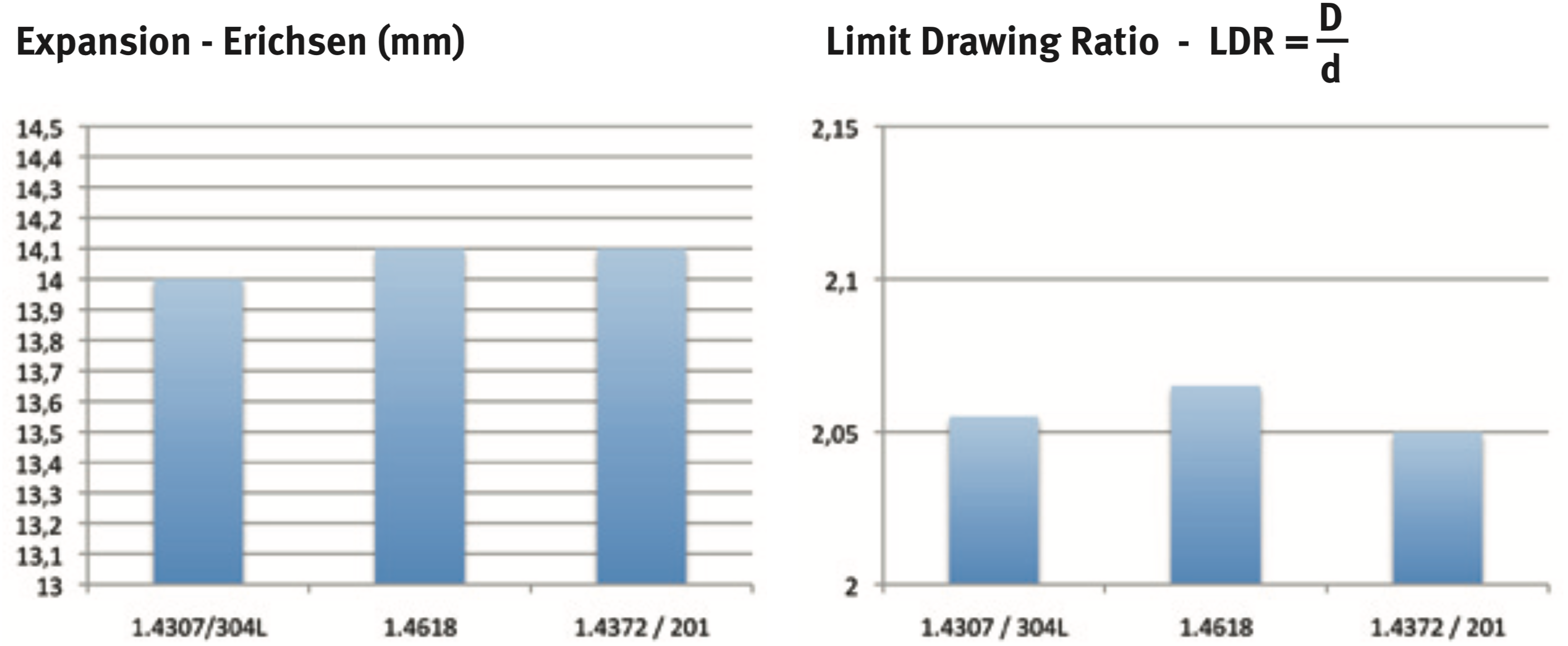
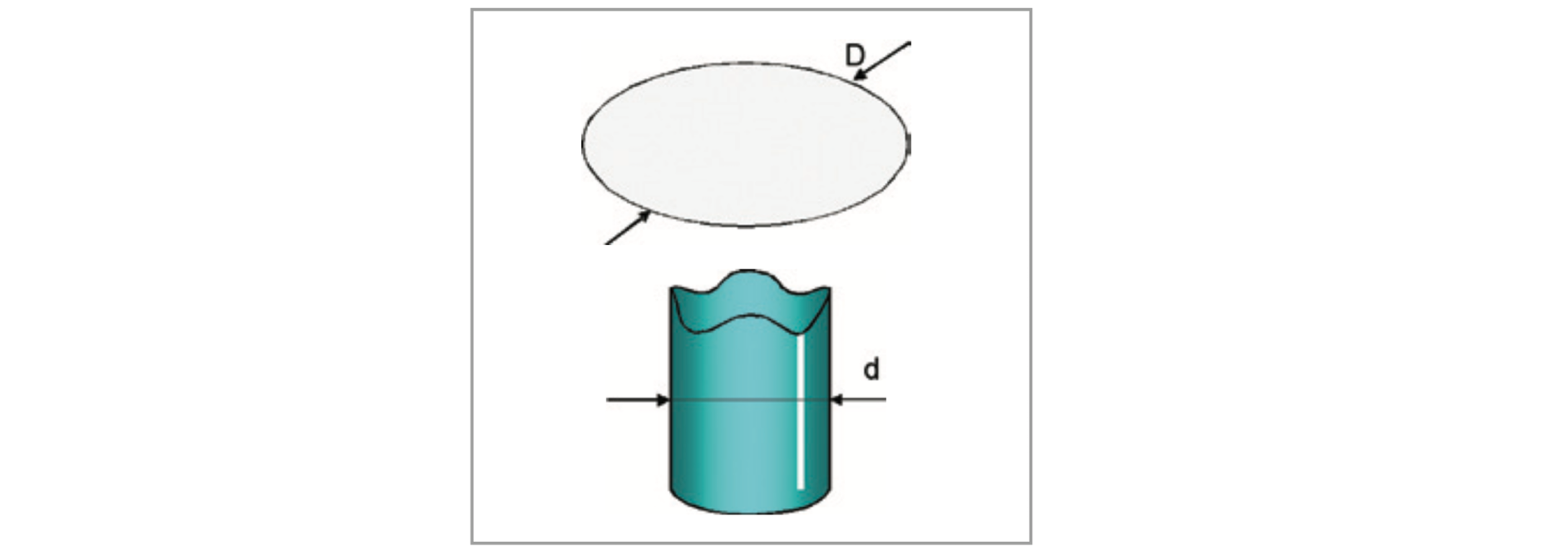
LDR values are improved compared with the classic 1.4372 (201) grade. The combination of minimum 1 % Cu additions and optimum nitrogen content obviously significantly improves the formability properties of grade 1.4618 compared to other 200 series grades.
The forming limit diagram, also known as the forming limit curve, is a direct and useful representation of formability. The diagram illustrates the biaxial combination of strain that can occur without failure. The area be- low this curve encompasses all the combinations of strain that 1.4618 can withstand.
To construct a forming limit diagram, an array of circles, often 2.5 mm in diameter, is imprinted on the surface of the sheet metal before forming. The individual circles become ellipses wherever deformation occurs, except in areas of pure biaxial deformation. The major and minor axes of the ellipses are then compared with the circles of original grid to determine the major and minor strain at each location. The forming limit curve is defined by strain combinations that produce failure.
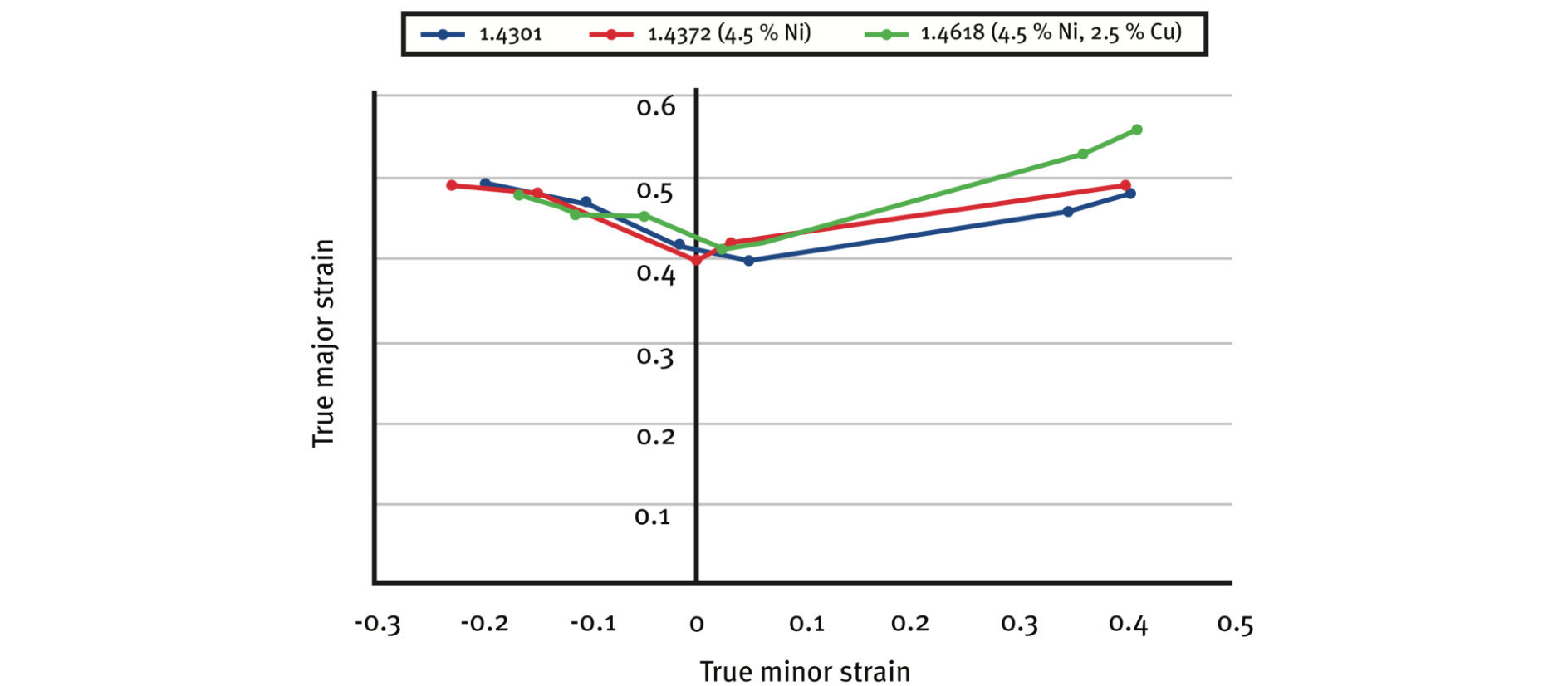
Delayed cracking is reduced by the chemical composition of 1.4618. The grade performs almost like grade 1.4301 (AISI 304). Salt spray tests performed on cups have shown, in the most critical areas, crack propagations for grade 1.4618 that are not observed for type 1.4301 (AISI 304) grades. Metallographic investigations have identified that cracks mostly initiate in corroded areas (small crevices, pits, etc.). This is consistent with results presented earlier that show a slight decrease in localised corrosion resistance when comparing grade 1.4618 with grade 1.4301 (304).
Swift cup test / Deep drawing ratio
Grade | Ni (%) | Cu (%) | 1.4 | 1.6 | 1.8 | 2.0 | 2.12 | 2.14 |
---|---|---|---|---|---|---|---|---|
14301 | 8.1 | 0.5 | + | + | + | + | + | + |
14618 | 4.7 | 2.4 | + | + | + | + | + | |
14372 | 4.4 | 0.3 | + | + | + | -- | -- | -- |
14372 | 3.6 | 0.3 | + | + | -- | -- | -- | -- |
“204Cu” | 1.1 | 1.7 | + | -- | -- | -- | -- | |
+ = Successful -- = Delayed cracking |
Table 3. Sensitivity to delayed cracking of some austenitic steels as a function of the deep drawing ratio, measured in Swift cup tests
6 Corrosion resistance properties
The pitting corrosion resistance of grade 1.4618 has been investigated by potentiodynamic-curve tests performed in a 0.02 M NaCl (23 °C, ph 7) solution (Figure 13). The grade behaves like grade 1.4310 (301), its pitting corrosion resistance being better than that of classical 201 grade but slightly lower than that of austenitic grade 1.4307 (304l). This is the result of a slight reduction in Cr content, partially offset by N additions, which enhance pitting corrosion resistance.
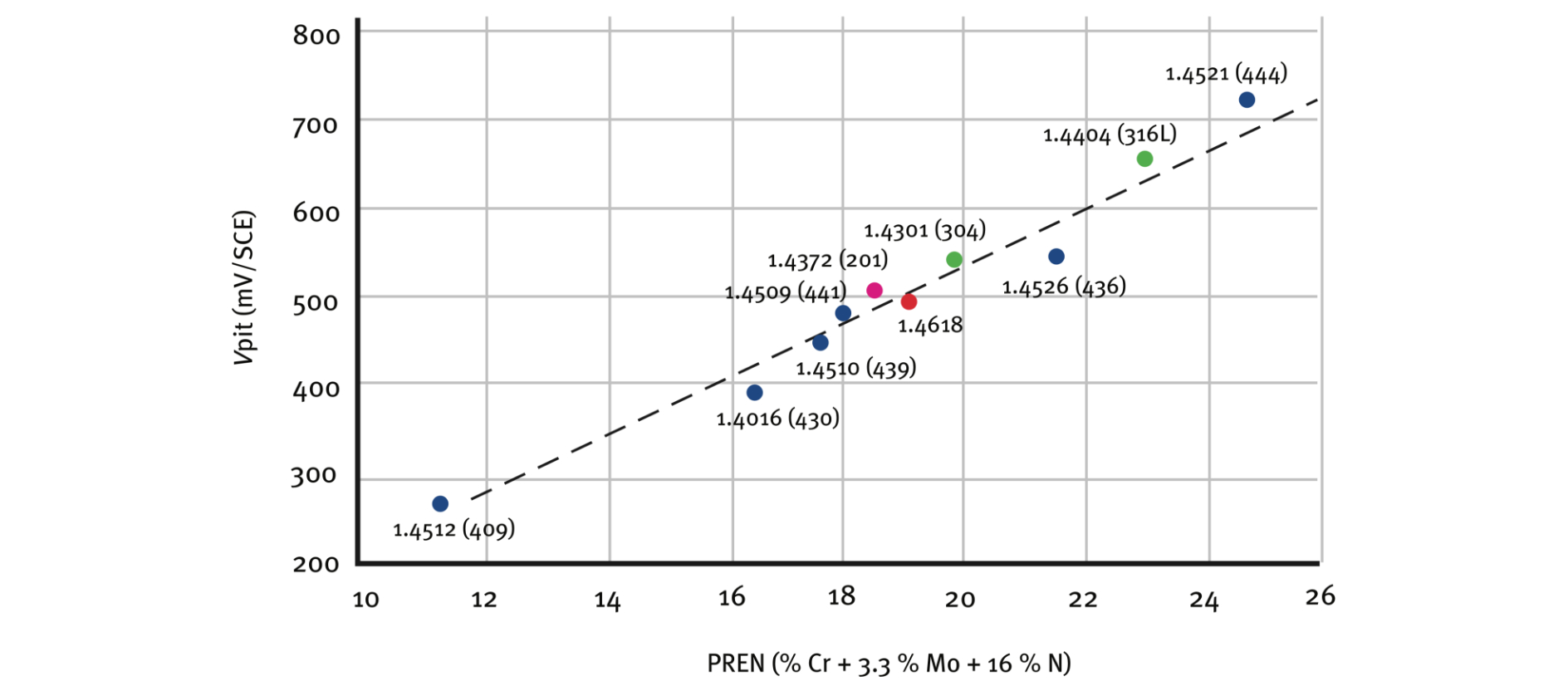
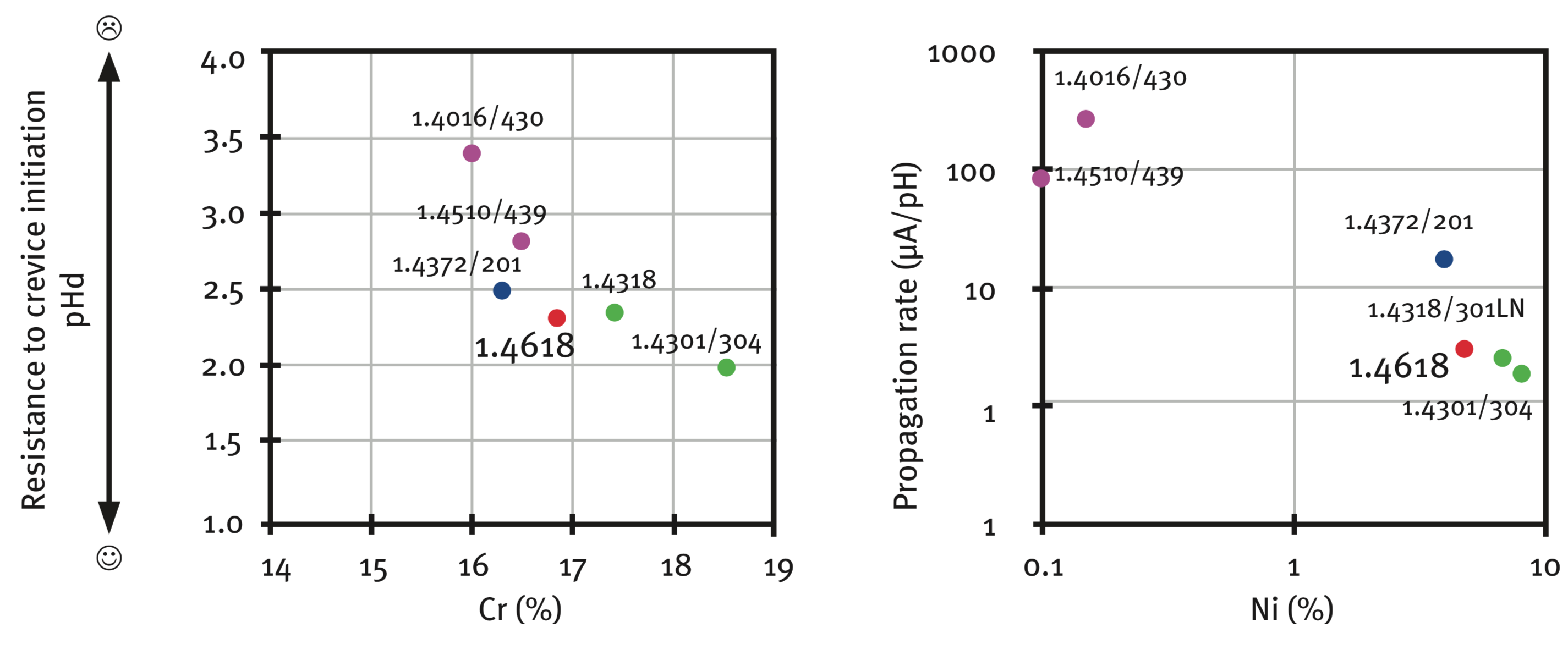
The crevice corrosion resistance (crevice initiation) of grade 1.4618 is significantly better than that of other 200 series grades. It is equivalent to that of 1.4310 (301) and very close to grade 1.4307 (304l).
With crevice corrosion, Ni has a powerful effect in reducing its propagation. With 4.5 % Ni, grade 1.4618 is more resistant to crevice corrosion than grades with lower nickel content. For both pitting and crevice corrosion resistance, grade 1.4618 is the best-performing grade among the 200 series grades investigated.
Intergranular corrosion resistance was investigated by means of EN ISO 3651-2 (Strauss tests). reducing nitrogen and carbon content improves the steel’s behaviour. Only sensitising treatments at 700 °C for 30 minutes followed by slow cooling induces intergranular cracks, after Strauss test and bending operations. In these conditions, even grade 1.4301 (304) is sensitised.
Grade | EN ISO 3651-2 | EN ISO 3651-2 | EN ISO 3651-2 |
---|---|---|---|
700 °C, 30 min + water cooling | 650 °C, 10 min + water cooling | 700 °C, 30 min + cooling 600 °C/h | |
14618 | |||
(0.05 % C, 4.5 % Ni) | pass | pass | fail |
14301 | |||
(0.05 % C, 8.1 % Ni) | pass | pass | fail |
14307 | |||
(0.02 % C, 8.1 % Ni) | pass | pass | pass |
14372 | |||
(0.05 % C, 4.5 % Ni) | pass | pass | fail |
Table 4. Intergranular corrosion testing conditions and results (Strauss test)
Stress corrosion cracking was tested in salt spray (fog), in accordance with ASTM B 117. With stress corrosion cracking, the initiation and propagation of cracks under the combined action of tensile stresses and a corrosive environment is described.
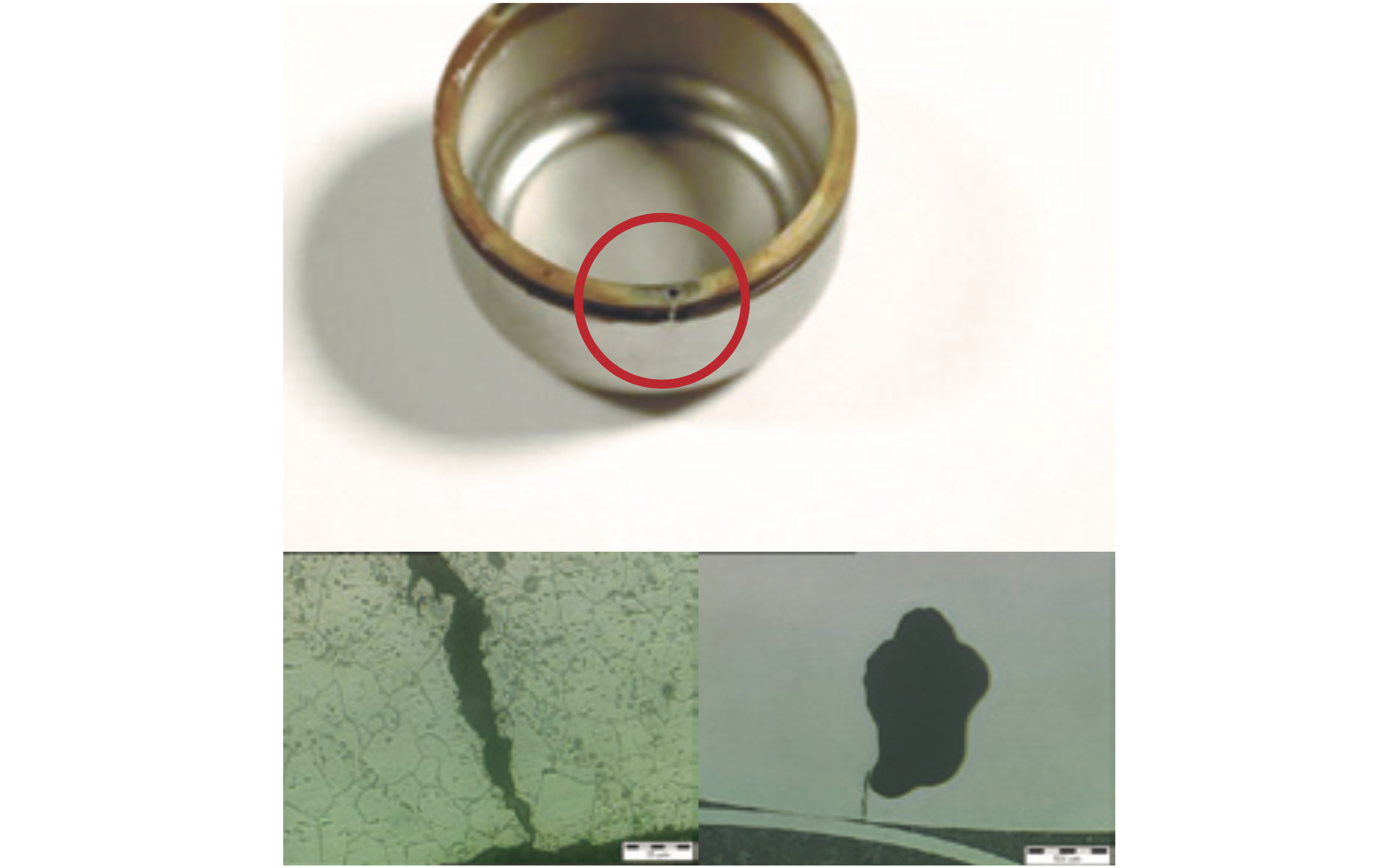
Steel grade | LDR | Number of cracks / Number of samples tested |
---|---|---|
1.4301 | 1.83 | 0 / 3 |
1.94 | 0 / 3 | |
1.4618 | 1.83 | 2 / 3 |
1.94 | 3 / 3 |
Table 5. Stress corrosion cracking results after 1000 h of exposure, in a salt spray (fog) test, according to ASTM B 117
7 Physical properties
Physical properties important for the successful implementation of stainless steels include coefficient of thermal expansion, electrical resistivity and specific heat.
The coefficient of thermal expansion is the change in unit of length (or volume) accompanying a unit change of temperature, at a specified temperature.
The electrical resistivity properties of grade 1.4618 rank between those of 1.4372 and 1.4301 austenitic alloys.
Specific heat is the quantity of heat required to change by one degree the temperature of a body of material of unit mass. Specific heat values for selected austenitic stainless steels are given in Table 8.
EN | ASTM | Mean thermal expansion coefficient (10-6 K-1) between 20 °C | and .. °C |
---|---|---|---|
T = 200 | 400 | ||
14618 | - | 17.4 | 18.5 |
14372 | 201 | 16.6 | 17.9 |
14301 | 304 | 17.0 | 18.5 |
Table 6. The coefficient of thermal expansion
EN | ASTM | Electrical resistivity (Ω·mm2/m) | |||
---|---|---|---|---|---|
0 °C | 25 °C | 50 °C | 100 °C | ||
14618 | - | 0.76 | 0.77 | 0.79 | 0.85 |
14372 | 201 | 0.80 | 0.81 | 0.84 | 0.89 |
14301 | 304 | 0.72 | 0.75 | 0.76 | 0.81 |
Table 7. Electrical resistivity
EN | ASTM | Specific heat (J/g·K) |
---|---|---|
39 - 41 °C | ||
14618 | - | 0.51 |
14372 | 201 | 0.51 |
14301 | 304 | 0.48 |
Table 8. Specific heat
8 Weldability
Table 9 shows typical welding conditions for grade 1.4618. grade 1.4618 behaves almost like grade 1.4301 (304). No specific welding parameters need to be observed and in most cases the same welding filler materials as for 1.4301 (304) or 1.4310 (301) can be used.
Welding process | Without filler material | With | filler | material | Protective gas |
---|---|---|---|---|---|
Typical thickness | Thickness | Filler | metal | ||
Wire rod | Coil | ||||
Spot welding Seam welding | <2mm <2mm | ||||
GTAW / TIG | <1.5 mm | >0.5 mm | Er 308 l (Si) W. Nr. 1.4370 Er 347 (Si) | Er 308 l (Si) W. Nr. 1.4370 Er 347 (Si) | Ar |
Ar + 5% H2 Ar + He | |||||
PAW / plasma | <1.5 mm | >0.5 mm | Er 310 | Er 308 l (Si) W. Nr. 1.4370 Er 347 (Si) | Ar |
Ar + 5% H2 Ar + He | |||||
Ar + 2% CO2 | |||||
GMAW /MIG | >0.8 mm | Er 308 l (Si) W. Nr. 1.4370 Er 347 (Si) | Ar + 2% O2 Ar + He | ||
Ar + 3% CO2 + 1% H2 | |||||
SAW | >2 mm | Er308l Er 347 (Si) | |||
Electrode | repairs | E 308 E308l E 347 | |||
Laser | <5 mm | He restricted: Ar–N2 |
Table 9. Typical 1.4618 welding conditions
9 Summary
See top.
10 References
[1] New 200-series’ steels: an opportunity or a threat to the image of stainless steel?, Brussels: ISSF, 2005
[2] Charles, Jacques, “The new 200-series: an alternative answer to Ni surcharge?”, Proceedings of the Stainless Steel USA Int. Conf., Houston, 2006
[3] The Ferritic Solution, Brussels, ISSF, 2007
[4] Charles, Jacques, "A new European 200 series standard to substitute 304 austenitics?", Proceedings, 6th European Stainless Steel Science and Market Conference, Helsinki, Jernkontoret, 2008, pp. 427-436
[5] Taulavuori, Tero, Ohlingschläger, T.,Säynäjäkangas, J.: "A novel view on material selection of stainless steels by optimizing material costs and product properties"?, Proceedings, 6th European Stainless Steel Science and Market Conference, Helsinki, Jernkontoret, 2008, pp.335-341
[6] ASM Specialty Handbook, Stainless Steels, Davis, J.R. (ed.), ASM International, 1996