Safer Seaming With Food Grade Lubricants
Good lubrication of can seaming machines is important for secure sealing, but there is an - invisible - risk of contamination if the lubricants are not suitable for food, and with possible serious consequences. This is why Fuchs Lubricants (previously Shell Lubricants) offers food grade solutions. These are already accepted by a major manufacturer and in comparative testing they perform as good and often better than competitive lubricants.
The sights and sounds of irregular can seams - hissing from fizzy drinks cans, dented cans and product leakages – are all signs that food packagers and can seamers desperately want to avoid. Poor seaming can quickly lead to a deterioration in product freshness and leave the food or beverage product open to contamination. Although these warning signs signal a problem, they present operators with the chance to take immediate action and minimise the immeasurable damage of a contamination crisis.
Unlike the threat of contamination due to poorly seamed cans, lubricant contamination does not offer the same warning signals; yet it can pose a greater risk to food quality and safety. Used to ensure the smooth and efficient running of can seamers, lubricants and greases can help to improve the regularity of the seam, increasing food safety. Better still, effective lubrication helps to reduce part corrosion, minimising the risk of food contamination through metal chips or rust. However, the use of non-food grade lubricants can quickly negate these operational and safety benefits, which is why Shell lubricants companies have developed a range of food grade can seaming lubricants and greases.
Non-Food Grade Risks
Many consumers would probably be shocked to learn that engine oils may have been used to seal their tinned foods. In many cases though, this is often the truth, as, for the past 40 years, general aviation piston engine oils have been widely used throughout the industry for lubricating can seamers. The oils have helped operators to overcome key lubrication challenges, such as high operating temperatures and speeds, enabling them to successfully lubricate the can seamers’ moving metal components and protect against expensive part wear and unscheduled stoppages.
As most can seamers lose oil during operation, non-food grade lubricants pose a very real threat to food safety. Total loss can seamers consume approximately eight litres (two US gallons) of lubricant per day, while recirculating systems can use up to four litres (around one US gallon) per day. Excess lubricant and grease can collect above the open cans on the seamers’ roll bearings or upper turret. This increases the risk of the lubricant and grease dripping or being flung off the seamers’ moving parts. If a non-food grade lubricant or grease enters the can before or while it is being seamed, the product is considered ‘adulterated’ and is therefore unfit for sale or consumption.
A Costly Crisis
A contamination incident at this point can prove a major problem for operators. Whole batches of products and packaging have to be destroyed and production lines stopped for long periods of time as can seamers are cleaned. Delays in production can lead to missed delivery deadlines, straining customer relationships and threatening repeat purchasing. Worse still, as the lubricant is seamed within the can, the contamination incident may go unnoticed until the product is on the shelf, endangering consumer health and welfare. By this time, further costs can be incurred, because of expensive product recalls and damage to hard-earned brand reputations.
Food Grade Safety
Operators can significantly increase food safety and minimise the impact of contamination with the use of H1 food grade can seamer lubricants and greases. Food grade products such as Shell FM Gear Oil TLS 150, Shell Cassida ® Fluid GLE 150 and Shell Cassida Greases, have been developed specifically for use in can seamers and have been formulated using a system of approved additives and base fluids. This composition means that the lubricants and greases are colourless, tasteless and odourless, and will not contaminate food if present in quantities less than the US FDA’s maximum permitted level for NSF H1 lubricants of 10 parts per million.
As oil in a total loss lubrication can seamer only stays in the machine for a relatively short period of time, Shell FM Gear Oil TLS 150 is based on a technical H1 white oil. This enables operators to effectively meet the continuous lubrication demands of the total loss system and protect the seamer’s components against accelerated wear, while reducing the threat of contamination through lubricant being flung off or dripping from the seamer’s components. For operators using recirculating systems, a synthetic food grade gear lubricant such as Shell Cassida GLE 150 can be used to maintain high levels of food safety and operational efficiency. The food grade qualities of Shell Cassida Grease RLS 1 and Cassida Grease RLS 0 will help to minimise the impact of contamination caused by grease drips from the seamer roll. Leading original equipment manufacturer, Angelus, has approved both Shell Cassida Grease RLS 1 and Cassida Grease RLS 0 for use in its can seamers.
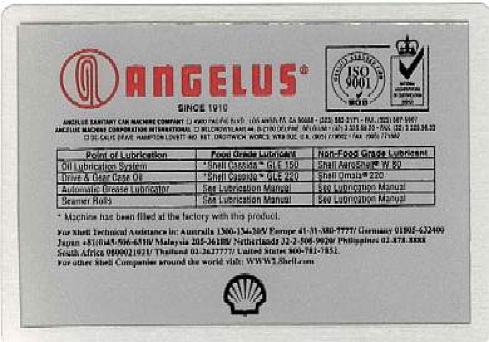
Safety and Performance - Shell Cassida products are the only food grade lubricants that Angelus recommends for use in its can seamers
Canning Without Corrosion
High-quality food grade can seamer lubricants can also offer excellent lubrication even in the presence of juice, water or food sauce. An effective canning lubricant will have high water-handling capabilities, allowing it to absorb free water. The removal of the water from the seamer reduces contact staining which can lead to heavy pitting (a common cause of bearing failure), rust and corrosion. While this enables operators to maintain continuous and reliable seamer performance, it also further improves food safety levels.
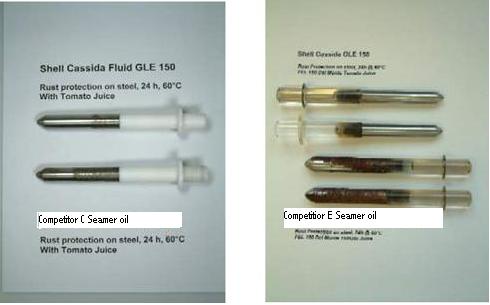
Heavy pitting caused by contact staining after water ingression. Product: Tomato juice
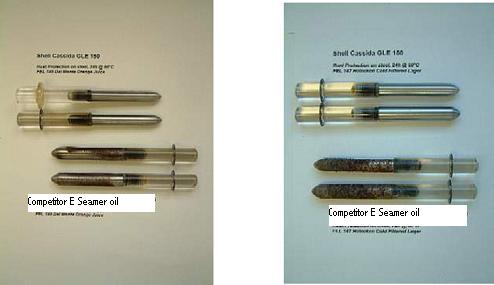
And in Orange juice and Beer
Protecting Process, Product and Brand
Open cans, high lubricant consumption and fast-moving can seamer components, all make the risk of accidental lubricant contamination during canning a constant threat. By using high quality, food grade, H1 approved can seaming lubricants and greases, operators no longer need to compromise food safety for lubricant performance. Effective food grade lubrication will help operators to improve can seamer cleanliness and achieve better seaming – having a positive impact on equipment uptime and the flow of cans down the production line – while helping reduce the adverse impact of contamination.
Soft Drinks Industry Winters
The rich history of Soft Drinks Industry Winters BV is now in its third century. Today, the bottling company is alive more than ever. With a flexible attitude and high quality standards it has become the largest Dutch soft drinks exporter. In addition, the lubricants of Shell Lubricants (taken over by Fuchs Lubricants) make the machines run optimally and food safe.
"You ask, Winters fills": that's the motto of Soft Drinks Industry Winters BV in Maarheeze (North Brabant, The Netherlands). The company is not directly known to the consumers: the company has never sold soft drinks under its own name. Still, it can look back on a long and rich history. When William Van Hooff laid the founding stone of his brewery on August 5, 1797, he could not have realised that it would become an international soft drink company in two centuries time. By inheritance to the next generations in the year 1873 Jan Winters came in charge. Since then, the brewery was known by his name. In 1918 the production of soft drinks started. Until 1958 Winters only had regional ambitions. Then the company expanded business and Winters became producer of world renowned branded as Seven-Up, Sunkist and Canada Dry. When the domestic sales of soft drinks stagnated, the sight was set on various foreign markets in the seventies. In 1978 the company became part of TLC Beatrice International Holdings. Together with the Belgian soda bottling Sunco, who belonged to the same group, it took over the French mineral water producer St. Alban in 1996. After a management buyout the holding company Sun Beverages Company emerged in 1998, comprising Winters, Sunco and St. Alban.
Contract filling
In 1989 the licenses for the production of Seven-Up and other branded products for the Dutch market ended. Since then all attention is directed to 'contract filling'. This is done on behalf of major international food companies, retailers and other commercial organizations. Winters fills cans for a range of soft drinks, energy drinks, mixed drinks, juices, waters and beers with well-known brands. Between 5 and 10% of production is destined for its own brands, such as Sun Cola and Orange, Party Cola and Orange, Provita multivitamin drink, Maresca mineral water and Megaforce energy drink. Nearly 95% of the volumes is exported worldwide and thus Winters is immediately the biggest Dutch soda exporter. Every year more than 500 million cans are filled, packed and logistically processed. Winters currently employs 120 people in permanent employment and dozens of seasonal workers. Production runs per working day in three shifts for 24 hours and during the peak season in a four or five shifts.
To realize such large numbers, Winters has three production lines. An important part of each line is the can sealing machine running at very high speeds. Two machines seal 1,200 filled cans per minute and the third will do another 625 units per minute. Frans Cox, head of utilities and engineering projects: "Such devices are very capital intensive. It is very important that they remain in good condition to produce an excellent product with a constant quality. "
For the reliability of the sealing machines the right food grade lubricants are essential. Some parts are lubricated with oil, others with grease. Oils are able to dissipate more heat and are regenerable by filtration. They are applied for the lubrication of (plain) bearings and gears. Fats are oils encapsulated in soap skeleton. They have less heat-dissipating properties, and can not be reused. The fats serve, inter alia, for the lubrication of bearings in hemming rollers. Incidentally, their lubricating frequency is lower than that of oils.
One supplier
Until ten years ago, Winters used lubricants from various manufacturers. F. Cox: "However, the need hasd arisen to rationalise the diversity of products and providers. To get a better overview, we decided to give one person decision-making authority and to work with just one supplier. The result is that if there are questions, there is only one firm where you can go to the right person. That's an advantage, because of the high speeds the machines are very sensitive and, if necessary, you should be able to rely on a rapid intervention of your lubricant supplier."
Arjan Nieuwstraten, food sector specialist of Shell Lubricants, adds: "The material of a modern beverage can is much thinner than before and therefore the method of sealing is more critical. So you can imagine the tolerances to have to work with will be smaller than before. The importance of the lubrication is thus become much greater. "
At that time Winters already bought around 70% of its lubricants from Shell Lubricants and, partly by this collaboration this supplier was chosen. "The people at Shell were always coming into action directly when needed. They were also always ready for the start up of new equipment, switching to newer oils or fats, assistance in making lubrication schedules, etc. That's why we did not have to think long about who we wanted to go into business with", F. Cox continues.
In practice, there is now a 'gentlemen's agreement' between the two parties. "A synergy has grown between our companies, based on years of trust", A. Nieuwstraten confirms. "The collaboration with Shell Lubricants is closely aligned with the expectations that we have with respect to our suppliers", F. Cox adds.
Incidentally Shell offers Winters an additional service with the Lubriplan software. This lubrication management system provides an accurate overview of the inspection points for fats and oils in the machines and generates user-friendly instructions. So it is indicated where and with what frequency there has to be checked or lubricated and with what product that needs to be done. "Moreover Lubriplan builds up a history of the objects to be lubricated. It may sometimes appear that periodic lubrication at a certain location is needed less frequent than planned. Such cost optimisations we do proactively for Winters", A. Nieuwstraten continues.
Food safety
In this industry, food safety is of paramount importance and it is essential that no contamination of the filled product occurs. The past decades mineral (engine) oils were used to lubricate can seaming machines. Because these are unfit and improper to come into contact with food, Shell Lubricants has developed a range of food grade oils and fats which are suitable for the lubrication of such equipment. They may be used in the food industry and meet the European standard and the US FDA NSF H1-H1. The FDA (Food and Drug Administration) considers incidental contact of these lubricants with the food product to be acceptable to a level of 10 ppm (parts per million). The lubricants are food safe without compromising on their lubricating properties.
Incidentally, there are two types of food grade products. In some sealing machines the lubrication takes place in a closed circuit: this process is called "recirculating oil '. For such systems Shell Lubricants has developed the synthetic oil 'Shell Cassida Fluid GLE' series. That series has excellent lubricating properties and is recognized by leading suppliers of sealing such as Angelus (USA), FMC FoodTech (Belgium) and Ferrum (Switzerland). A second process is that wherein the lubricant is used only once: the "total-loss system. For this, Shell introduced the food grade mineral oil 'Shell FM Gear Oil TLS 150'. That delivers outstanding performance, even in the presence of water, juice or beer. Moreover, this oil absorbs water, preventing rust.
Remarkable is that these Shell products were developed in cooperation with Soft Drinks Industry Winters. A. Nieuwstraten: "We gave attention both to food security and to the optimization of lubricant performance. At Winter we have gained a lot of knowledge about the lubrication of sealing machines with these products and numerous tests have led to the most sophisticated lubricants for this sector."
Quality Systems
Large beverage producers that have known branded products manufactured through contract fillers not only value high the quality of the final product. Also, the extent to which the production process is controlled and hygiene risks are avoided, plays a major role for them. Winters has responded and holds international quality certificates according to ISO 9000, 14001 and HACCP (hazard analysis critical control points). In addition, the bottling company is certified to the BRC standard (British Retail Consortium). That standard contains guidelines which food producers have to meet in order to supply the large English supermarkets. Finally, for German and French retail chains Winters has the IFS certificate (International Food Standard).
With the high quality food grade lubricants of Shell Lubricants and the high quality standards of Winter the consumer profits.
Featured expert: Pieter Van de Schepop