Coffee Milk
Coffee milk, also known as evaporated milk or coffee creamer, is a thickened, often sweetened, homogenised and sterilised milk, that is intended for use in coffee. Traditionally, hot boiled milk was added to the coffee to soften its flavour. Using cold milk would cause the coffee to lose too much of its heat. This is where the idea of thickening the milk has sprung from, making it possible to directly add the milk to the coffee. Coffee milk has a thicker texture compared to regular milk, and a higher fat-percentage. Besides whole milk coffee creamer, there is also a semi-skimmed and skimmed coffee milk with a lower fat and sugar content.
Coffee milk production process
Two processes can be distinguished: in-bottle (in-packaging) sterilisation and in-flow (line) sterilisation. In the following paragraph the in-bottle sterilisation process of coffee milk will be discussed more thoroughly, and the in-line sterilisation method will only be discussed briefly.
In-bottle sterilisation
Raw ingredients
The raw milk, used to produce coffee milk, should not contain any acids or other metabolic products in high amounts. The germ count must be low, making the milk easier to sterilise. Furthermore, the raw milk should not contain any colostrum, given that this would make the product less heat stable. Using infra-red, the fat and protein content of the raw milk is measured.
Standardisation
In the past, there were legal requirements in the Netherlands, about the the fat and (non-fat) solid content of coffee milk:
- Whole coffee milk: at least 7.5% fat and at least a solid content of 25%
- Semi-skimmed coffee milk: between 4 and 4.5% fat and at least a solid content of 24%
- Skimmed coffee milk: less than 1% fat and at least a solid content of 20%
For this reason, before further processing is carried out, the milk is standardised. Since only water is removed during the evaporation process, the concentrated milk should already have the desired fat to non-fat solid content ratio. Standardisation is achieved by adding skimmed milk (milk, of which a part of the cream has been removed); or sweet buttermilk (a by-product of the butter production); or whey (a by-product of cheese-making), to the raw whole milk, until the desired ratio is obtained.
Pre-heating
After standardisation, the milk is intensively pre-heated for about 1-3 min at 100 to 135°C, in a plate or tubular heat exchanger, in order to:
- Kill off pathogenic microorganisms and a large part of the heat-resistant microorganisms and bacterial spores
- Deactivate enzymes
- Increase the heat stability of the evaporated milk
- Reduce the chances of thickening of the evaporated milk when it is stored
- Raise the temperature of the milk in preparation of the first stage of the evaporation installation
- Enhance a certain flavour perception (caramelising the lactose)
The precipitation of the heat-labile protein, from the milk serum onto the casein protein, causes the heat stability of the milk to increase. This serum protein layer prevents the coagulation of the casein micelles during the sterilisation process. In addition, the pre-heating process decreases the quantity of dissolved calcium and phosphate, which has a favourable effect on the heat stability of the product.
After pre-heating the milk is whiter in color, this is due to the fact that the pre-heating causes the serum proteins to denature, and thereby enabling the light to scatter more.
After pre-heating, the milk is cooled to about 70°C.
Evaporation
Using a rotary vacuum evaporator or falling film evaporator, the milk is concentrated down to a solid content of about 31%. Over-concentrating lowers the yield and heat stability of the thickened milk.
By creating a vacuum, the boiling temperature of the milk is lowered to 65 to 70°C, while ensuring that the milk will not get a cooked flavour, and scorching is prevented. A lower temperature results in a risk of thermophilic microorganisms to grow.
Homogenisation
In order to prevent the evaporated milk from creaming during long-term storage at a higher temperature, the thickened milk is homogenised with a two-stage high pressure homogeniser. This process takes place under a pressure of 125 to 250 bar, at a temperature of about 60 to 65°C. Homogenisation increases the viscosity, which in turn decreases the heat stability. The Homogenisation should, therefore, not be carried out too intensively. Homogenisation increases the whitening power of the coffee milk in coffee.
Cooling
After Homogenisation, the milk is cooled to a temperature of 8°C using a heat exchanger. Next, the non-fat solid content of the milk is checked, and if necessary, standardised with water. It is important to note that adding the stabilising salt solution of 10%, causes the milk to dilute again. The milk is then temporarily stored in insulated tanks until the desired amount of stabilising salt is determined.
Stabilising
In order to ensure that the thickened, homogenised coffee milk does not coagulate during sterilisation, a stabilising salt (usually Na2HPO4) is added. Because the stabilising salt is basic, it increases the pH of the coffee milk. In addition, the salt binds a part of the present Ca2+, causing the casein protein to carry a larger negative, repelling charge. Both changes provide an increased heat stability. Since there is a difference between batches of milk, a trial sterilisation is usually performed on small batches to determine the right amount of stabilising salt. After this step, there is the possibility to add additional vitamins to the coffee milk.
Packing
After the addition of the stabilising salt, the coffee milk is filled in glass bottles or tin-plated cans. These cans are provided with an internal lacquer layer in order to prevent the iron or tin from ending up in the product. Before the cans are closed off, steam is blown into the upper part of the can (headspace) to limit the over-pressure during the sterilisation process.
Sterilising
The cans and bottles are then sterilised in a rotary autoclave or continuous sterilisation system for 15 to 20 minutes at a temperature of 110 to 120°C. When the desired Sterilising effect has been achieved, the products are cooled down to storage temperature. Through Maillard reactions (caramelising), the coffee milk becomes browner in color. The color can be changed, by applying a different temperature and time combinations. Moreover, sterilisation increases the viscosity of the coffee milk.
Labeling
The packages are labeled and packed into shipping units. When the coffee milk is stored at a temperature of between 0 and 15°C, it will have a longer shelf life.
In-flow sterilisation
The production process for in-flow sterilised coffee milk is similar to that of in-bottle sterilised coffee milk, up until the Homogenisation step. Since in-flow evaporated coffee milk is UHT sterilised, there is no need for intensive Homogenisation. Homogenisation serves in this case only in order to prevent the coffee milk from creaming. After Homogenisation, the milk is cooled to a temperature of between 5 to 8°C and stored temporarily. The Homogenisation step may even be omitted, if the entire process is carried out in one go. Because temporary cold storage tends to increase the risk of further thickening the coffee milk, the latter method is preferred.
The coffee milk is sterilised at a temperature of 122 to 140°C UHT for 4 seconds to 8 minutes with the aid of a tubular heat exchanger. Generally, it is not necessary to add salt to stabilise the coffee milk.
After sterilisation, the coffee milk is aseptically homogenised to reduce any protein aggregates that may have been formed. After the product has been cooled, it can be aseptically filled into various containers. After which, the coffee milk can be stored for 6 to 9 months at room temperature.
Food Safety & Hygienic Design
The preparation area must at least comply with GMP: being visibly clean before use, and no long-term presence of water remaining after cleaning.
Pre-heating is one of two critical steps in the production process to kill off any microorganisms. It is important that this part of the production process is well designed - according to EHEDG-directive no.1. During pre-heating, a plate heat exchanger is often used. It is known that these plates even when new, but even more likely after some time, will start to leak. Regular inspection is key in order to make sure highly deformed thin plates of the plate heat exchanger do not suffer from stress and corrosion in along the splits and cracks.
After pre-heating, the whole line, including filling machine, must be hygienically designed: meaning cleanable to microbial level. Unless the product is pasteurised after filling, GMP is sufficient. The evaporator has to be hygienically designed, because the product is circulated above the evaporator for a longer period of time, and there is a risk of the formation of heat-stable thermophilic microorganisms, which are, at a higher storage temperature (tropical), also able to grow after sterilisation.
However, at GMP, the sterilisation of the packaging is still not a license to be less careful during the pre-processing phase or cleaning the processing equipment less frequently or not fully, or extending the production run. Large amounts of heat-stable toxins, coming from microorganisms, may still be toxic after sterilisation. In particular, toxins of S.aereus can remain, and will pose a threat to consumer health
Hygienic cabling at a Unilever factory
The Streamline HD cable support system was explained at a knowledge event. After internal consultation, Ben & Jerry's decided to get started with it. The initial findings are so positive that they are going to prescribe their suppliers to use this form of cabling from now on.
“My boys were quite envious when they heard where I was going”, Michael Evers—Business Development Manager at Niedax Group and Secretary of the national working group Hygienic Cabling— told us, while standing in the reception hall of Ben & Jerry’s factory in Hellendoorn.
It all started in the 1950s; in addition to bread and pastries, Hellendoorn baker Gerrit Valk, decided to start producing ice cream. In the 70s, the production site was moved from the centre of Hellendoorn to its current location in Hellendoorn, and was increasingly automated. In the 90s, the company stopped baking. Unilever took over the factory in 1985 and started producing Ola ice cream. Since 2002, the core business of the factory has been producing Ben & Jerry's ice cream. Ben & Jerry's is a great example of a factory where all kinds of brownfield-projects run and have been run in order to produce in a state of the art manner.
.jpg)
In the reception hall, we meet Leon ter Braak—QA Officer at Ben & Jerry's Hellendoorn— who has worked at this location for 17 years. We take our seats in the Strawberry Cheesecake room. The smaller Peanut Butter room was occupied. Smaller? Yes, but the peanut products are more popular. Leon has just completed a validation of the factory as one that produces products with and without peanuts.
Leon explains that the work of a QA Officer involves many things. FSSC 22000 requires that necessary measures are implemented with regard to food fraud and food defense. The entrance gate was moved, a fence was placed around the building, and identification was required upon entry. ‘Cleaning and disinfection’ were also an important part of the FSSC 22000. However, appropriate measures were already in place because milk and milk free products were produced on the same production line.
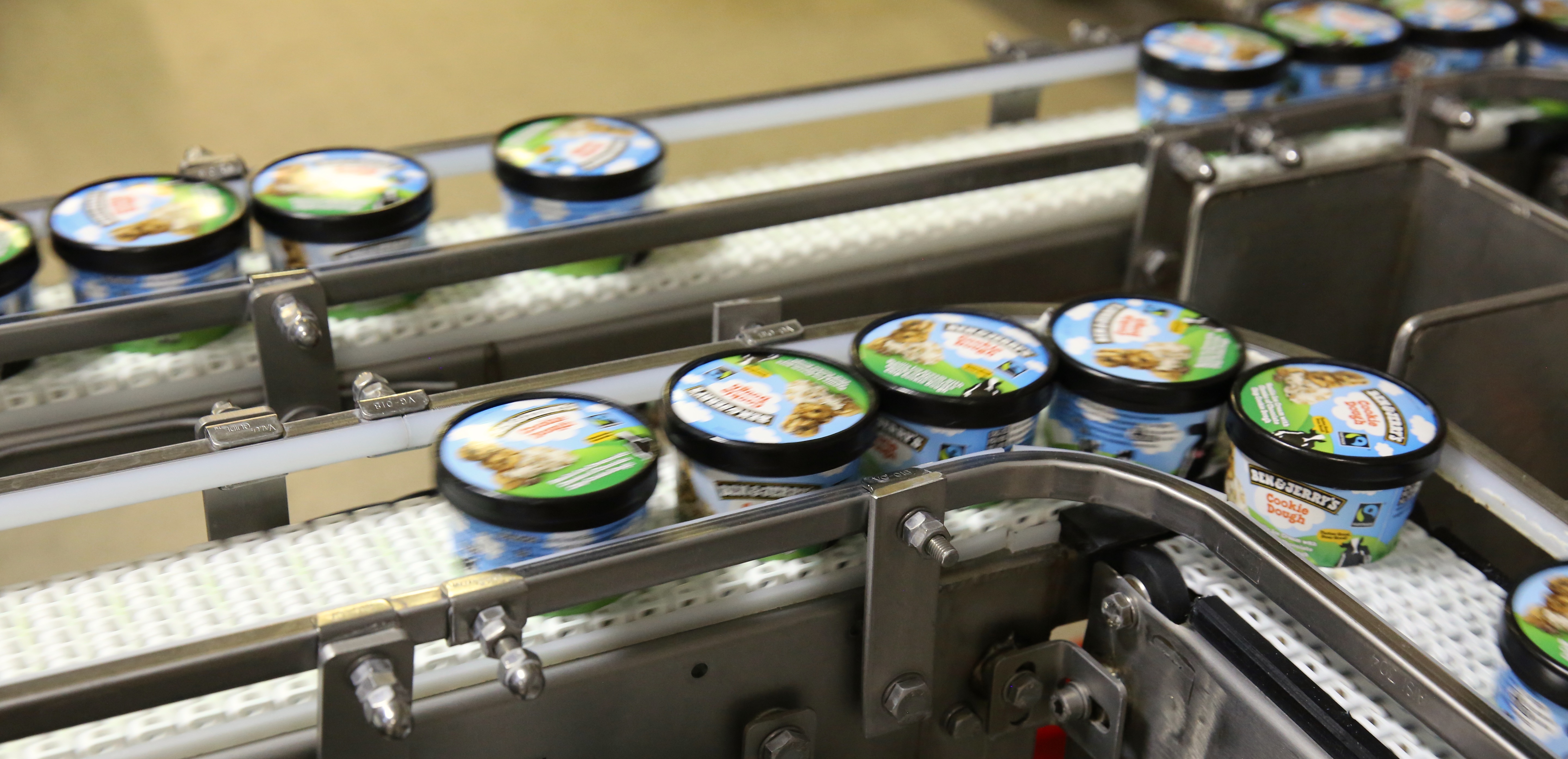
Hygienic design? The FSSC 22000 is not specific in this area. Leon points out: "You trust that the supplier of the machines will supply them in accordance with the EHEDG Guidelines. Of course, the machines are tested and assessed before use by our Project Engineers. We see that most issues arise with our own in-house modifications to the machines.”
In regard to food safety, quality concerns always revolve around four things: microbiology, allergens, chemistry and foreign parts. There is always something to improve. An example is the current way in which cables are attached to the equipment. It is not easy to clean around cabling—a prerequisite for controlling microbiology. Cable ties become brittle and break over time due to frequent cleaning. Pieces of cable ties, including the metal detectable ones, cannot always be detected. Yet, Leon cannot recall ever having received a complaint about this. Nevertheless, you always want to prevent it from happening.
Recently, Leon attended a Knowledge Event on Hygiene in the Food Industry, organized by Safe Food Factory and held at the Technische Unie. Leon went with the idea that “this can be interesting, even though I may not have the technical knowledge”.
The alternative of securing cables with a spring instead of cable ties, which was presented at the event, was a good idea to implement at the factory. The Quality Department manages the improvements at Ben and Jerry's Hellendoorn and has a dedicated budget for this. A team was formed immediately, and Gouda Holland (part of the Niedax Group) was invited to give an in-house presentation together with the line engineer involved. "When he recognized the practical benefit as well, he submitted the idea to the MT and they approved it," said Leon. "Now the first three items have been placed on one of the machines at a critical location above the six open packages. The first steps have been taken. Two cables still need to be extended and other parts like cable trays need to be adjusted too, but priority is given to the inside of the equipment. The first reactions are positive. It looks sleek. The cables run neatly, and you have room to clean”.
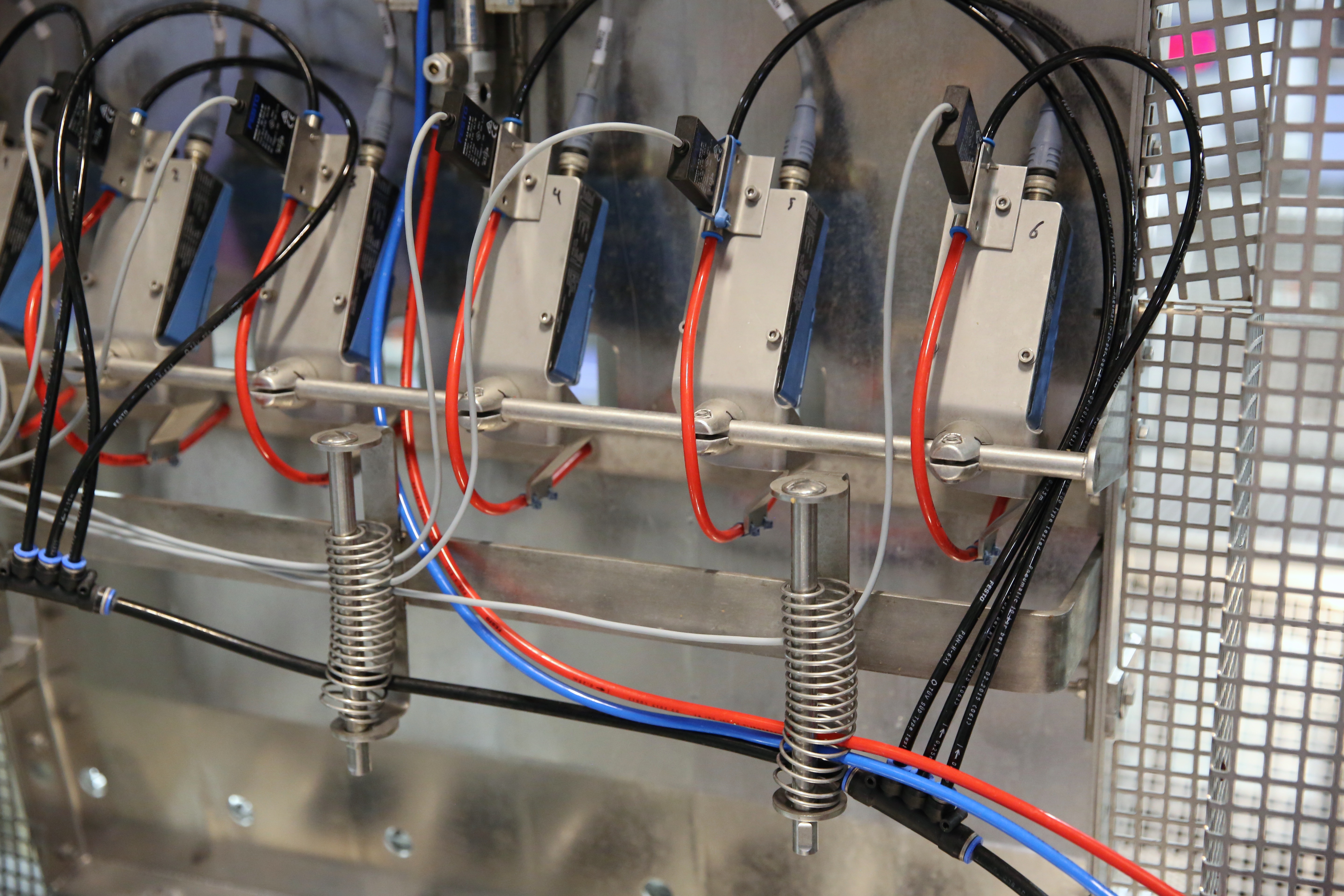
Saving by investing. Leon explains; "Upgrading an existing installation with Streamline HD will pay for itself. It makes the installation more flexible and easier to maintain. This just saves the Technical Department a lot of time and work".
What does the future look like? Leon continues; "I really like the solution from our supplier Selo for new equipment. The last unit Selo had not wired in this way. Selo now consistently applies the new cabling method throughout each machine. We are also going to make this wiring method compulsory for new equipment - and step by step, we are going to renew existing installations.”
Featured expert: Michael Evers